Last year — or was it the year before that (how time flies) — when we were working on Popo’s living room, I put insulation over the top of the sliding doors. I couldn’t get to the whole width, because part of the wall was in the hallway. I never got round to installing it, so now we are working on the office, this was the last chance.
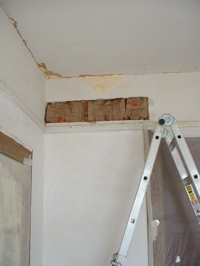
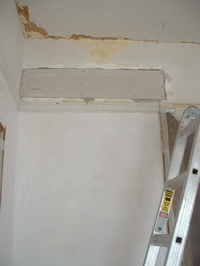
Above left, I’ve cut out a piece of plaster, and shoved insulation between the joists. Above right, gyp board on, and starting to repair the plaster.
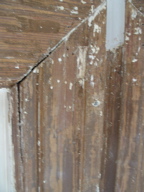
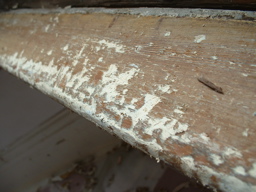
After stripping the paint off the window frames, some parts are in quite poor shape. The window sill (right) seems to have lots of notches taken out of it. Not sure how this happens? Because of settlement (left), the casing on this window is split, and the corner does not fit. There are also many holes where different curtains have been screwed to the frame.
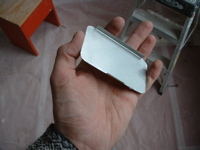
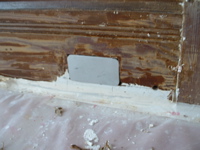
Janeen, when she was stripping paint off the baseboards in the living room, discovered that if your trowel slips into the plug while you are working (accidentally), it makes lots of sparks, and burns a hole into the trowel and plug. This time, I made a sheet metal cover that clips over the plugs so that I can protect them (and me) while stripping the paint off the plug. Worked great!
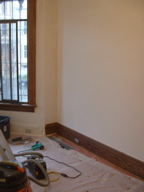
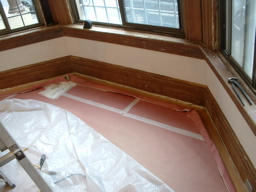
Working around the room, it’s exciting when the wood starts to reappear under years of paint. Most of the trim in this room is in very good shape.
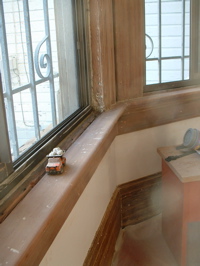
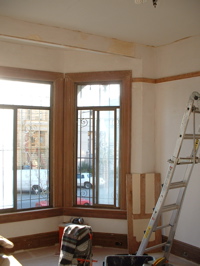
After sanding and filling, the window frames are starting to look really nice. It’s almost ready for stain.
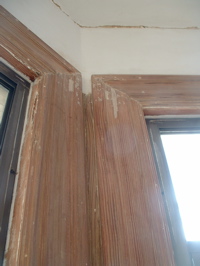
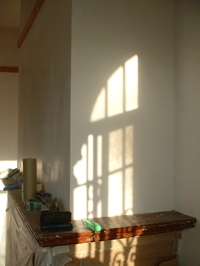
Above left is the casing that was split. I took it off, glued and clamped it, re-mitered the corner, nailed it back in, filled, and sanded. Slow work. The sun looks really nice in this room in the afternoons. I’ve also stripped the paint off the mantle shelf.
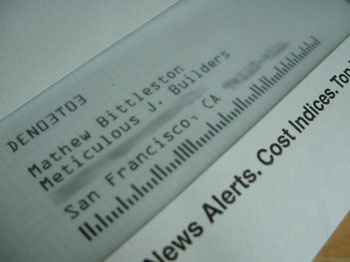
Hmm. How did this happen? I wonder if there’s a market for a meticulous builder?
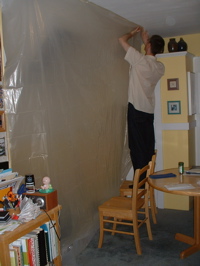
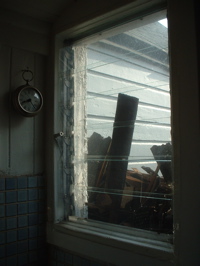
We’ve been planning to replace the roof for a couple of years, almost. Last year, we just didn’t have enough money to pay for it. This year, there hasn’t been four straight rain-free days since before December. Wednesday evening, we got a phone call saying the contractor would be here at 7:30 the following morning to start! I put up plastic and moved our table away from the skylight, which is being replaced.
When they arrived, it was a storm of activity. I had to go to work, but Janeen took the photo above right. They tore off three or more layers of roofing by lunch time.
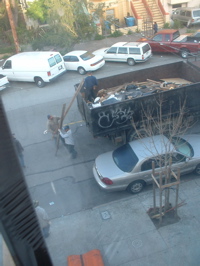
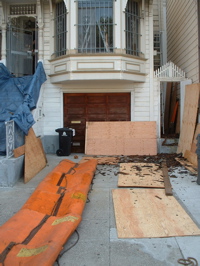
The photo above left shows one of the two dump trucks needed to haul away all the debris. In front of our house became a regular construction zone. If you look at the photo above right, you can see the ladder inside the windows of Janeen’s office. Nobody parked in our driveway that day: there was stuff flying everywhere off our roof. I think there were twelve people on our roof simultaneously.
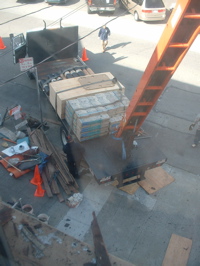
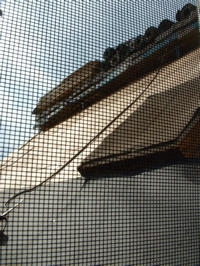
To get all the roofing off the roof, the contractors used a big orange chute. Well, for the stuff that didn’t go flying in all directions. To get new shingles and plywood onto the roof, they used a truck mounted conveyor belt. Above right you can see all the shingles piled onto the top of the roof, the plywood is installed, and they are starting to put the underlayment on. This is the end of day one.
At this point, I called the contractor. He was supposed to be installing a new skylight. It is bigger than the old one, so new framing is needed, but they haven’t done any framing, and are covering everything up with plywood and roofing already. I told him they are going to need to strip off the plywood, so they can install the skylight. He told me not to worry, everything is under control, and if they need to take off the plywood, they’ll do that…
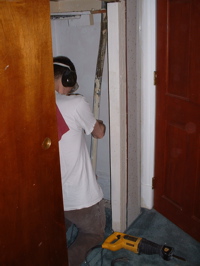
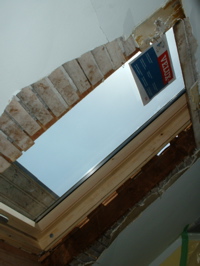
Above left, I’m taking out an old abandoned pipe that fell through into the closet when they were stripping off the roofing.
At the end of day two, the roofers walked in with the skylight, and said: The skylight is bigger than the opening (duh?), so they are going to just lay it on top of the roof and the opening will be smaller underneath! I told them they had to reframe, so that the skylight fit into the opening properly. That’s the last I saw of them. When I called the contractor, he sounded flustered. Seems the roofers had not understood that they were installing a larger skylight.
The next day when I got home, they’d partially reframed the opening, and set the skylight on top still (the opening is still too narrow). They then proceeded to try to seal up outside, but the manufacturer’s flashing did not fit (because the skylight is supposed to fit into the opening, not sit on top of the roof). The roofers adhered a bunch of roofing goop around the flashing, nothing was fitting properly, so they jammed everything in place and left.
Well, that lead to a “nice” meeting between me, the contractor, and the roofers. Apparently, when cleaning up after nothing was fitting, a bunch of “extra” parts got thrown out, so they can’t even install the skylight properly until they re-order those parts. Right now, it’s temporarily waterproofed for the rain, and the contractor is ordering new flashing and parts. At this point, I’m rather disappointed that the roofers didn’t read the installation instructions (I did!), as they’ve obviously not installed one of these skylights before (at least not properly).
The contractor is being extremely helpful, and keeps promising that he’s going to make sure it’s all done right. He’s made sure everything is temporarily water tight, and the roofers have always cleaned up very well. We’ve had no leaks, and he’s not asked for a penny until it’s all complete and we’re happy. It’s just a pity this skylight is turning out to be such a pain. If I did this again, I’d install the skylight, and let them do all the roofing. Everything would be done by now. Lesson learned.
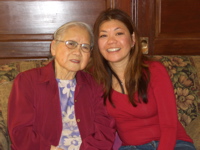
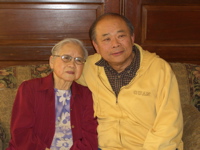
Popo got some special visitors: Her brother-in-law Willy (Popo’s sister passed away last year), and her niece Kimberly came by for a visit.

And it was Janeen’s birthday! Her cake was two Black China Bakery vegan cupcakes.